What can a games manufacturer offer to the world during a global pandemic? How can a company that has been around for half a century change its course in the proverbial blink of an eye, repurposing factories to produce life-saving face shields for health workers in the front line?
These were questions Cartamundi faced when Covid-19 hit the USA. On 20 March, all U.S. factories were closed, with all their employees furloughed. But it didn’t take long for a bright idea to arise.
“We asked ourselves: what can we do to give back to society and to help fight the virus?” says Philip Wauters, Executive Vice President of Cartamundi USA. “With an acute nationwide shortage of protective materials for frontline healthcare workers, we decided to design, manufacture, and donate face shields to the organizations that need them the most.”
What happened next was a North American team effort for Cartamundi, with close cooperation between the Design Centre in Seattle and the factories in Dallas, Texas, and East Longmeadow, Massachusetts. “And with the utmost attention to the health and safety of our employees”, Wauters is quick to add.
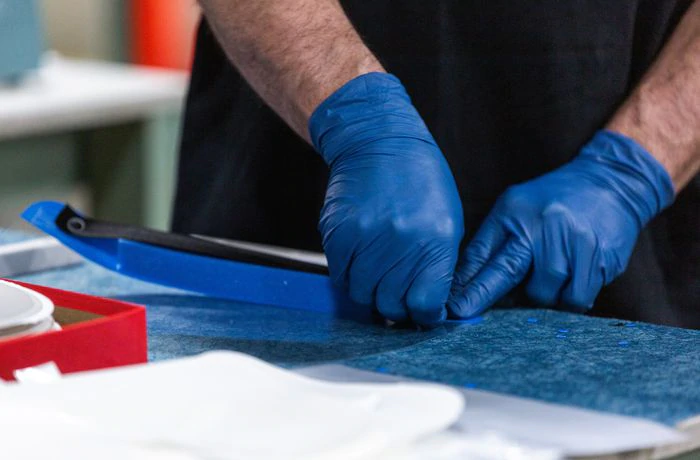
Cartamundi USA is now producing face shields in two U.S. locations. Every week, tens of thousands of face shields will be donated to hospitals, health care workers, and first responders. The donation is made in partnership with Cartamundi’s customers Hasbro.
This is the story of the proud people who make it all happen.
A very natural step
Let’s fly all the way to Seattle, Washington. Home to a thriving gaming community, Seattle is where one of the Cartamundi Design Centre is located. A block and half away from its biggest client, the games company Wizards of the Coast, known for Magic: The Gathering among other classics.
It is no coincidence that the Design Centres and Wizards of the Coast are so close together, according to Stefan Congram, for Cartamundi in Seattle. “We’ve got a bit of a triangle going on between the Design Centre, Wizards of the Coast, and the Dallas manufacturing facility,” says Congram. “I make sure that all the information goes all the way around the triangle.”
The design of new products, the streamlining of production processes, coming up with creative ways to show people exciting new tech and materials: this is common practice for Congram and his team. Since the Design Centre opened in 2017, it has been responsible for developing exciting packaging for games and creating lasting, affordable experiences for game enthusiasts.
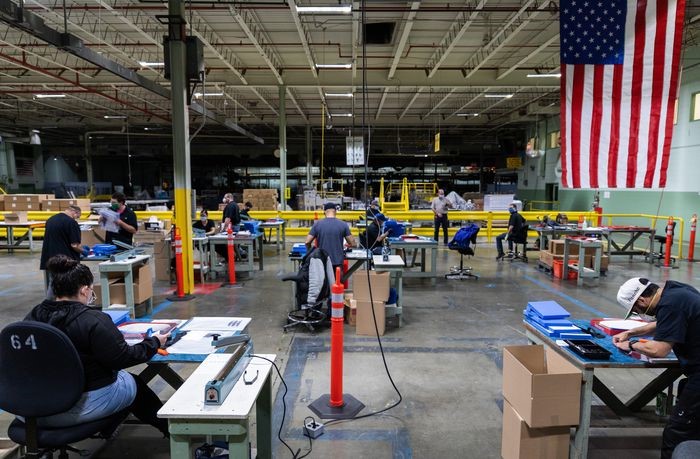
But that all seems to be miles away from the designing of face shields. Or is it?
“It is a leap, in a way,” Congram concurs. “But we do so much in our office. We’re not only used to working with paper, but also with plastic, and injection molded pulps and foam. We are very familiar with all of the materials that are used on the face shield, as individual components. So this was a very natural step for us. The only new thing was the elastic band that holds the shield in place.”
Still, Congram was presented with a challenge when Philip Wauters asked him to design, develop, and prototype a face shield that can be produced quickly and easily, both in Dallas, Texas, and in East Longmeadow, Massachusetts. He didn’t start from scratch, but it took some creativity to get it right.
“We used open-source documents that were already approved by the FDA (Food and Drug Administration), and then we altered those component lists to fit the materials we currently had in stock.”
48 hours of truth
Congram likens the designing of the face shields to US game show Top Chef, where contestants have to prepare dinner or dessert with a mystery basket of ingredients.
“Speed was essential. Healthcare workers need these face shields as soon as possible.”
– Stefan Congram, Cartamundi –
“We had to work with whatever we had floating in the cupboard,” says Congram. “Currently, in the US, and probably all around the globe, there are shortages of not only PPE (personal protective equipment) but also of the raw materials. That is because the supply chain for many of the materials has either completely collapsed or ran dry.”
“Under normal circumstances, to make a face shield, I would just pick up the phone and order whatever I need. But as soon as I started designing the face shields, it turned out that the materials weren’t easily available. The sourcing teams in Dallas and East Longmeadow then had the important task of finding these materials in large quantities.”
Congram finished the design and prototype of the new face shield in less than 48 hours. Quite remarkable, considering that it would usually take a full month. “Speed was essential,” says Wauters. “Healthcare workers need these face shields as soon as possible.”
From Seattle to Dallas and East Longmeadow
The designs were reviewed by the factories in Dallas and East Longmeadow and production started there on April 9. “The face shields will be produced in Dallas and East Longmeadow because we wanted to make sure we took care of the needs in both Texas and Massachusetts”, says Wauters.
Face shields are considered essential business because of the shortage all over the world. “One could argue that games are essential too because they give us something fun to do while at home and because they contribute to our mental wellbeing,” says Wauters. “But according to the law they’re not essential, so we can’t produce them now.”
Guaranteed health & safety at the workplace
It did take some preparation to get all work stations ready. “Working with a traditional conveyer belt was not possible because of the need to maintain a safe distance,” says Congram. “That’s why we installed all-inclusive individual work stations. Employees have everything they need on hand to assemble a complete face shield, without moving around. And each work station is separated by plexiglass screens.”
Wauters also stresses that every effort was done to guarantee the health and safety of all employees. “We run very secure facilities,” he says. “As soon as our employees enter the building, they are subjected to a touchless temperature check. If they register too high, they go to a confined area and get a re-test after 20 minutes. If they still register too high, they exit the building and go to see a doctor. Only after a negative COVID-19 test, it’s safe for employees to return to work.”
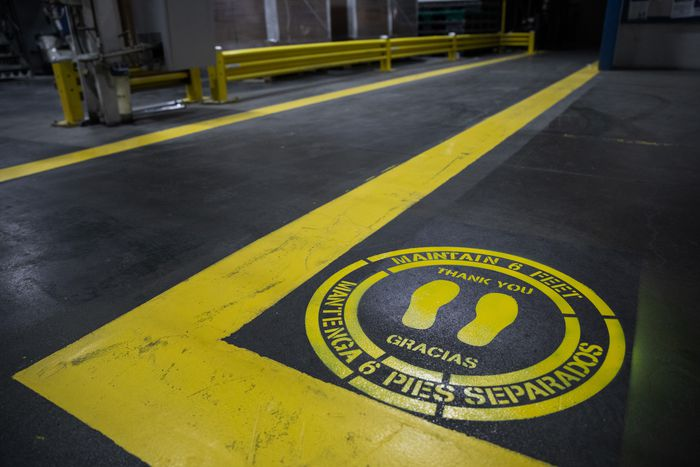
At the first signs of the pandemic, mid-March, Cartamundi implemented very stringent safety measures worldwide, some of which are even more strict than local regulations.
The recently re-opened factories take the protection of the workforce to an even higher level, as Wauters explains: “Gloves, sanitary gels, and other protective measures are provided to staff. We have separated the shifts in the factory to reduce the contact. Social distancing is implemented throughout the facilities. The factory is cleaned thoroughly after each shift. And canteen services are suspended.”
“I’ve never been so humbled in my life to know that a company like Cartamundi cares so much about its employees and about the community.”
– Stefan Congram, Cartamundi –
Proud to be giving something back
As soon as Cartamundi USA started working on the face shields, a tremendous sense of pride spread across the organization.
“We’ve given our employees something to care for and be proud of,” says Congram. “From the stories that I’ve heard, everybody that is working on the face shields is proud. Some even requested: ‘Hey, can I have one while I work to keep myself safer?’ There’s going to be merit in that. Knowing that your employees are motivated and happy to produce something like this is rewarding in itself.”
As for Congram, his love for Cartamundi, which was already big, has grown tenfold in the past few weeks. “I’ve never been so humbled in my life to know that a company like Cartamundi cares so much about its employees and about the community. I’m truly thankful for that.
Fighting the pandemic, creating hope
The face shields that Cartamundi USA manufactures will help protect healthcare workers and other people from droplets. They should be used in combination with other protective clothing and safety measures recommended by the government and the World Health Organization.
“If there’s still a need after the initial batch we will continue production for as long as it is necessary.”
– Philip Wauters, Cartamundi –
“Starting in the week of 20 April, tens of thousands of face shields will be donated to hospitals, health care workers and first responders in the greater Dallas area, in close cooperation with the Dallas County government,” says Wauters. “Cartamundi will also start the production and donation of face shields from its factory in East Longmeadow, Massachusetts. All in close cooperation with our customer Hasbro” Elsewhere in the world, in Waterford, Ireland, Cartamundi started assembling essential medical test kits in the board games facility.
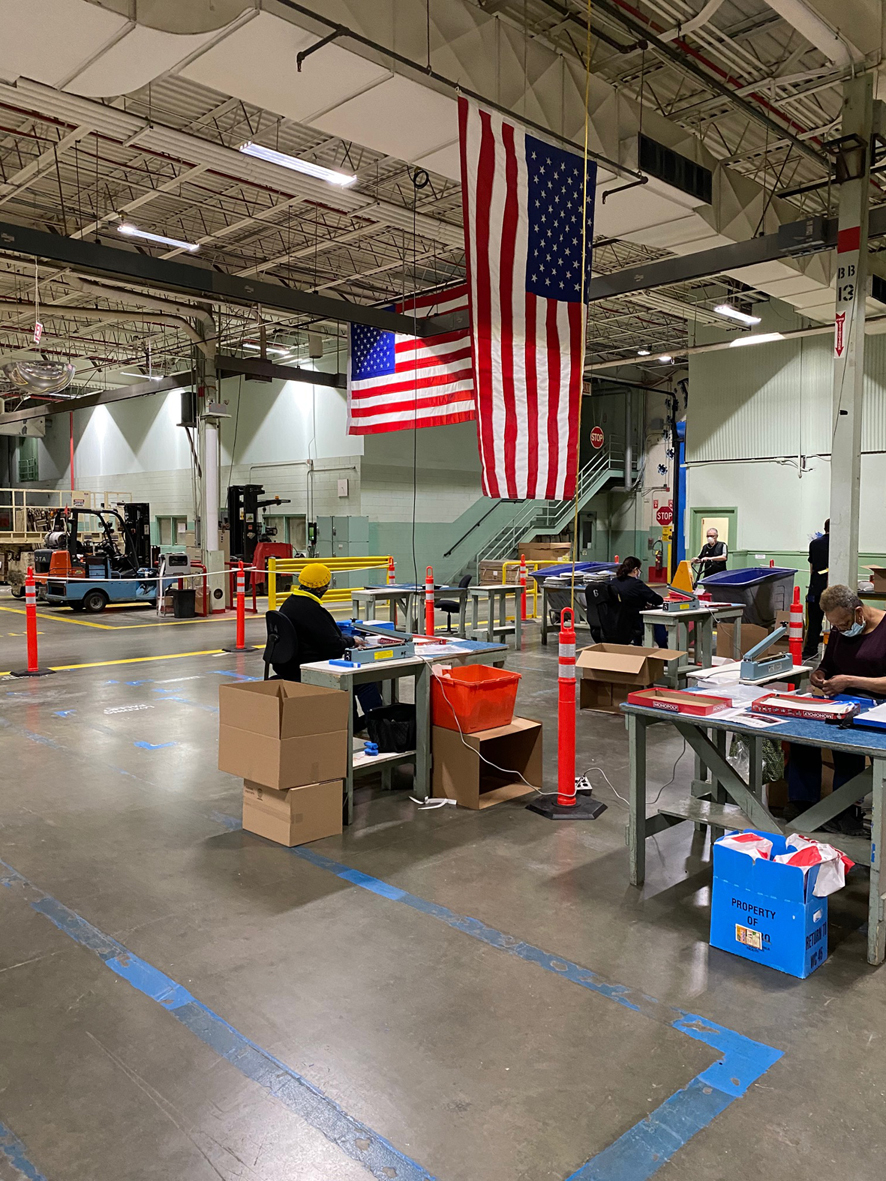
What will happen when Cartamundi has completed the planned production face shields? “If there is still a need after the initial batch, we will continue production for as long as it is necessary,” Wauters promises.
In the meantime, the company is looking ahead to the coming weeks.
“This is a global crisis that no-one has ever seen in their life and hopefully will never see again,” says Wauters. “We have prepared the factories to fully re-open as soon as the government restrictions are released.”
“Fighting the pandemic is what matters now,” Wauters concludes. “And we’ll be doing everything in our power to support those healthcare workers on the frontline.”